FSW Plants - ECOLOGICAL & ECONOMIC
FSW Plant Linear (OptimusP)
The linear friction stir welding machine is used for longitudinal welding of pipe shell sections. The fully automated welding process of the plant is easy to operate by one operator. After loading and setting up the system with the parts to be welded, the process starts without any further intervention. The friction stir welding process takes place in four steps:
1. The FSW tool, consisting of a pin and a shoulder, penetrates the pre-positioned sacrificial part with the rotating pin until the necessary depth is reached. Once the pin has reached the necessary depth, pressure is applied to the surface of the sacrificial part by means of the shoulder. The friction between the shoulder and the part surface builds up the necessary process temperature.
2. After a short dwell time, the feed motion starts and the welding tool moves in longitudinal direction to the pipe casing piece.
3. in order not to leave any undesirable end crater caused by the pin penetrating into the parts to be welded, another sacrificial part is positioned at the end of the pipe casing piece, in which the welding is finished.
4. After removing the now longitudinally welded pipe section, the sacrificial parts are cut off and the pipe section is rounded again to ensure the required roundness.
During the welding process, the operator has the possibility to follow the welding on a monitor. The control system also makes it possible to record and evaluate the parameters of the welding process. After the welding process, signals or information on the status or on the identification of the parts can be output if required. Adaptations according to customer specific requirements for integration into a modern production line are possible.
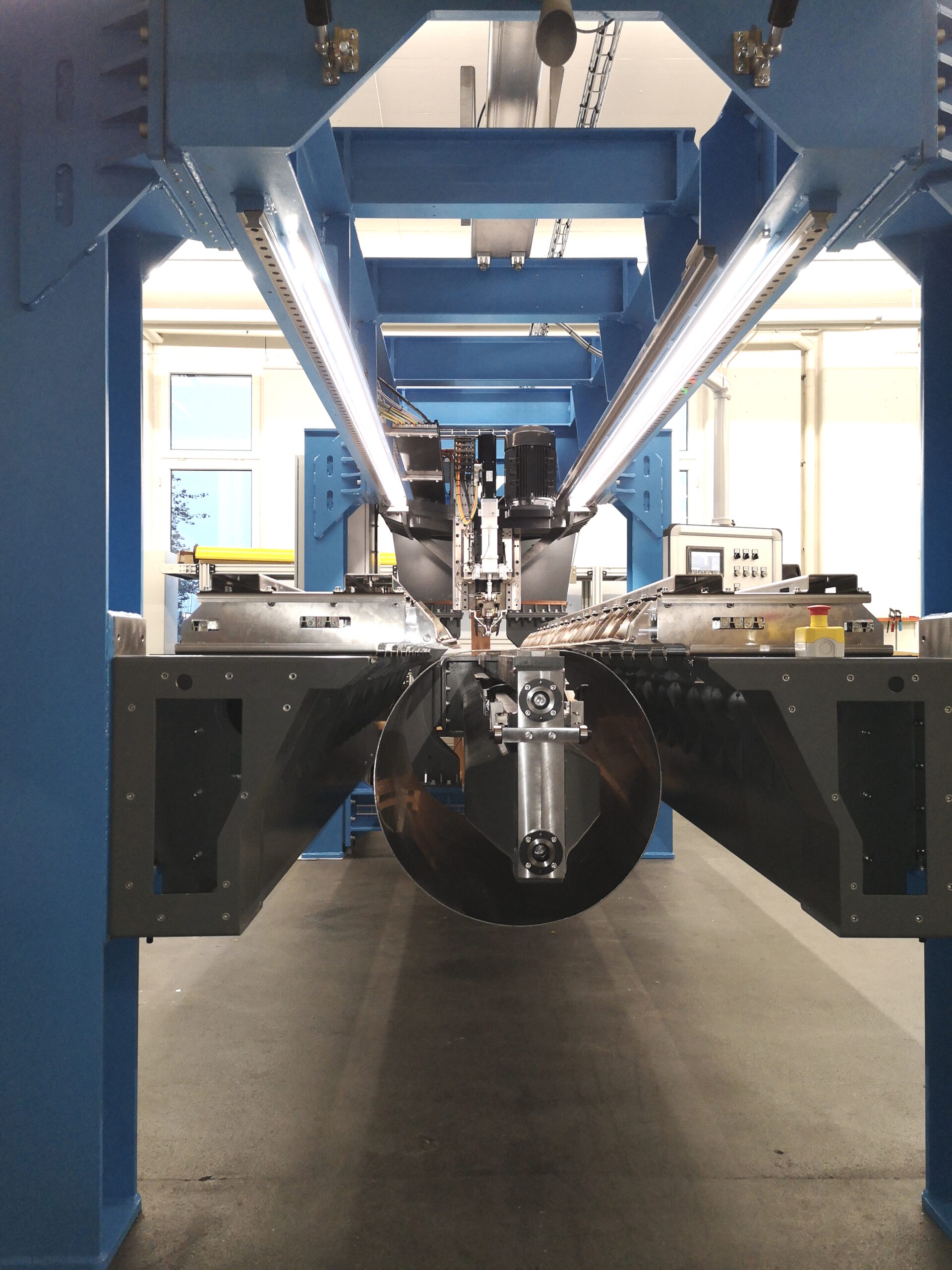
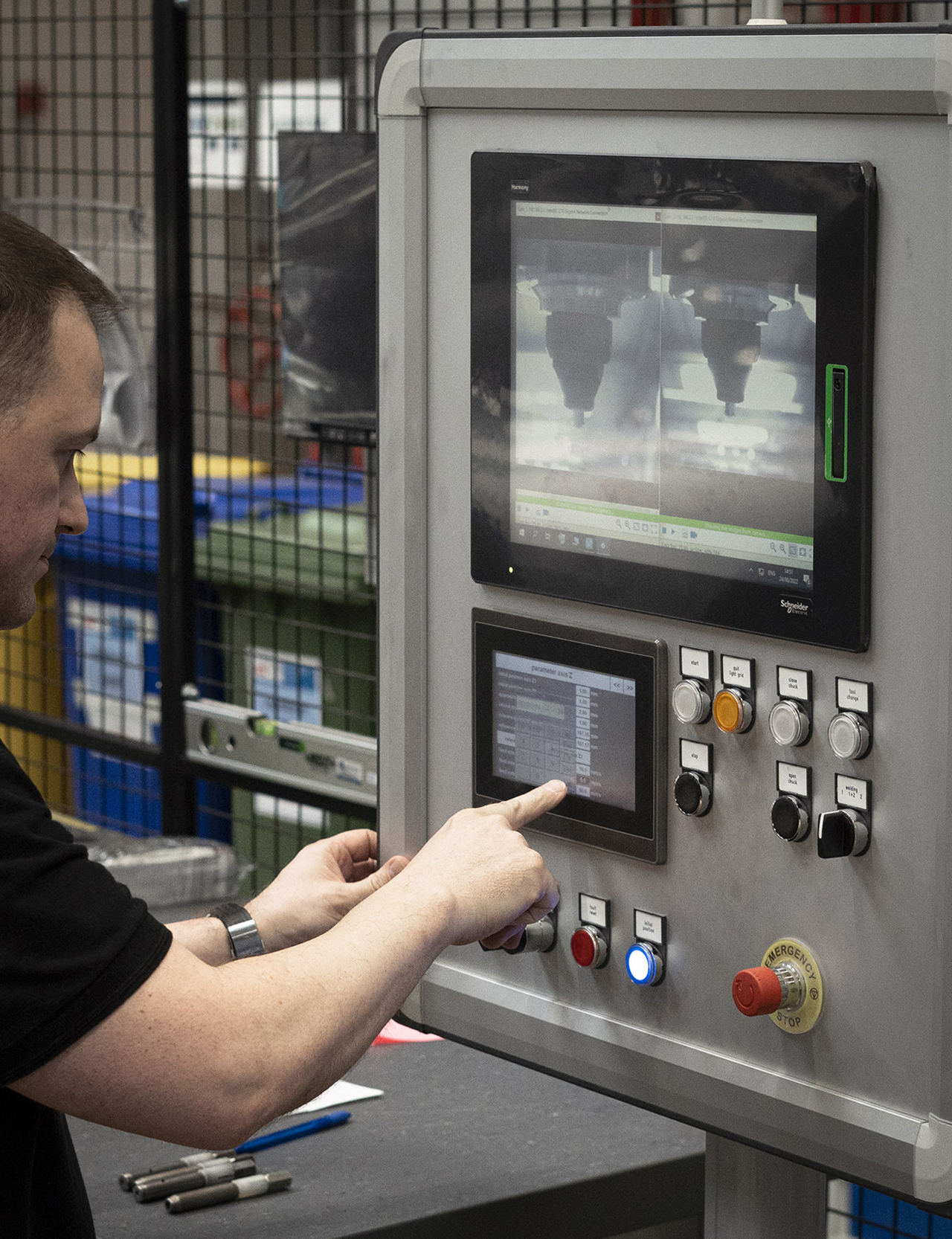